Use of two highly efficient technologies from IMS Messsysteme GmbH installed in one measuring system enables thyssenkrupp Rasselstein GmbH to further reduce roll damage and broken strip
Heiligenhaus, November 2024
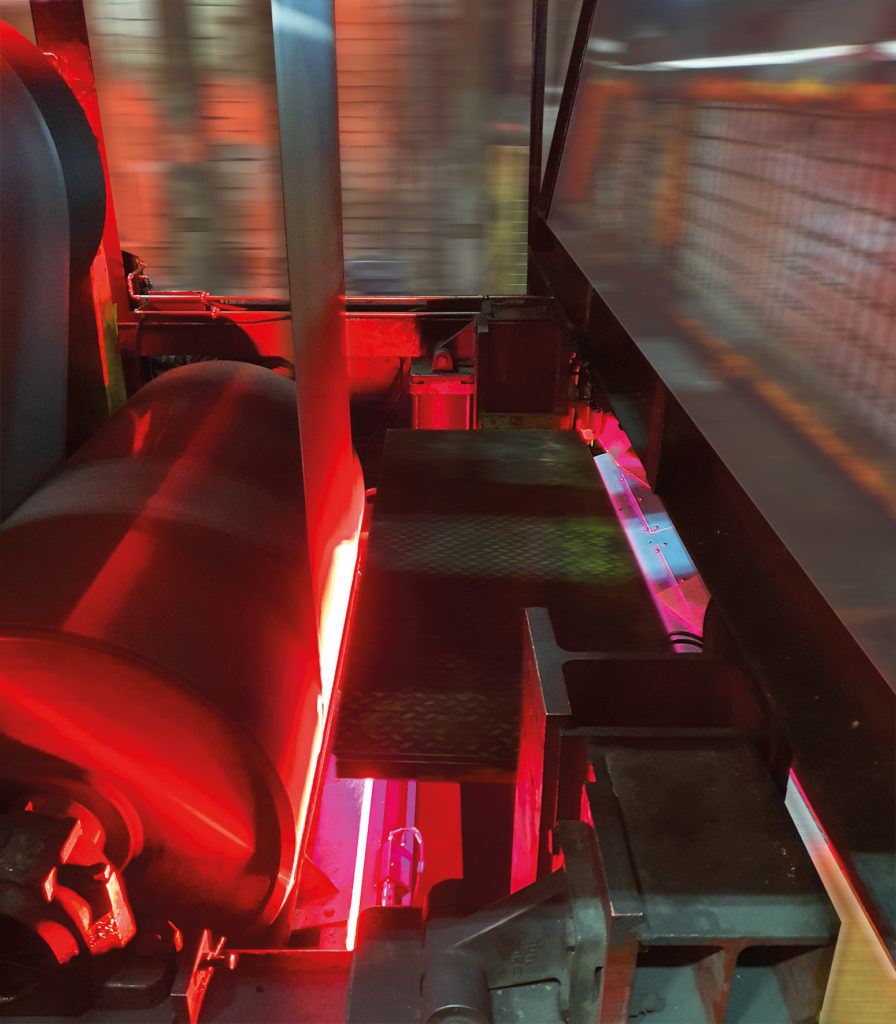
- Simultaneous detection of surface defects and their visualisation both in 2D and 3D
- Reliable assessment of surface defects through evaluation of image and height information
- Significant reduction in roll damage and broken strip through reliable rejection of critical defects
IMS Messsysteme GmbH, Heiligenhaus, and thyssenkrupp Rasselstein GmbH, Andernach, have reached another milestone in their constructive, decades long business relationship:
Installed for the first time in a pickling line, the combined 2D/3D surface inspection system of the global market leader IMS was successfully put into operation in November 2021 at thyssenkrupp Rasselstein in Andernach, the world’s largest production site for packaging steel.
"thyssenkrupp produces the packaging steel of the future – efficient, process optimized and sustainable. rasselstein® packaging steel stands for material grades in premium quality which are continuously further developed in close cooperation with our customers."
(Source: www.thyssenkrupp-steel.com)
At thyssenkrupp Rasselstein, pickling is the first processing stage of the hot-rolled strip on its way to fine sheets with thicknesses from 0.100 to 0.499 mm. Optimally, surface defects are already detected on this starting material and thus at an early stage in order to be able to guarantee the usual high product quality of the rolled products.
At the same time – in addition to the perfect quality of the hot-rolled strip – serious problems such as broken strip and roll damage are successfully avoided in subsequent processing. For this reason, thyssenkrupp Rasselstein GmbH has been using state-of-the-art inspection systems to check the surface quality in its pickling line for many years.
However, past practice has shown that surface defects can only be detected with conventional inspection systems by way of their visual appearance.
Basically, however, it remains difficult to make a correct statement about the surface quality of the product when it is inspected by the human eye.
"Despite the use of modern detection and classification technologies, an uncertainty in quality assessment remains due to the surface condition of the pickled hot-rolled strip and the occasional occurrence of pseudo defects, such as scale and water, in systems with conventional line scan or matrix cameras, which can never be completely eliminated even with the collection of large amounts of training data. In contrast, defect detection using height measurement can be used productively in a very short time, as only numerical threshold values for critical defect depths need to be defined. The depth of the defect is usually the decisive criterion for the severity of a defect. Nevertheless, it is of course still possible to train a classifier for a more fine-grained differentiation of the defects."
explains Björn Krämer, Head of System Technology Image Processing at IMS Messsysteme GmbH.
Just get
in touch.
You are interested in our combined 2D/3D Surface Inspection System for pickling lines?
Great! Let’s talk about.
Please do not hesitate to contact me if you require technical information or further explanations.
Sincerely,
Thomas Köpsel
Sales / Product Manager SURCON Surface Inspection Systems
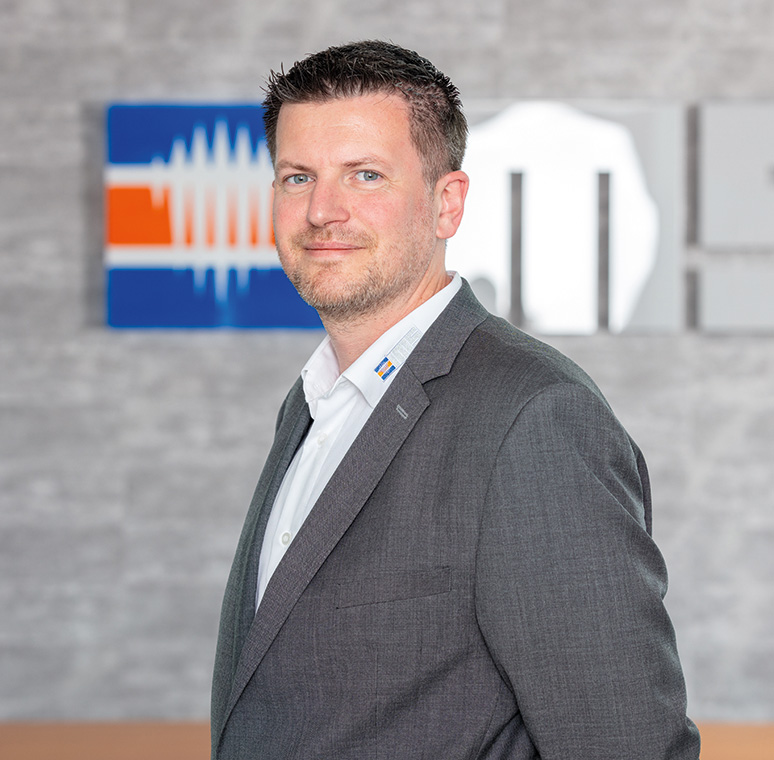
Phone
These circumstances gave rise to the desire on the part of thyssenkrupp Rasselstein for fully automated, reliable and objective defect detection in the running process. Here, too, the long-established German company once again opted for the proven measuring technology of the world market leader IMS Messsysteme GmbH for its quality assurance.
With the newly implemented 2D/3D surface inspection system in the pickling line, thyssenkrupp Rasselstein is once again setting new standards in the industry.
IMS started developing surface inspection systems as early as 2008 and delivered the first functional 3D inspection system for slabs in continuous casting as early as 2010.
Further fields of application for heavy plates, tubes and the inspection of complex profiles were also developed within a short period of time.
The idea of using this technology for the first time in pickling at thyssenkrupp Rasselstein already led to revolutionary results in the field study. Immediately there was a clear improvement in the automated detection of serious surface defects in the running process and, as a logical consequence, a significant reduction in the damage and failures caused by this.
"Together with IMS, the idea arose to use the proven 3D technology in the pickling process as well in order to reduce the effects on the subsequent rolling process through automatic detection and depth measurement of the defects and thus to minimise disruptions caused by broken strip or roll damage. These considerations were confirmed by a test installation, so that a productive system was installed in a short time. Since it was commissioned, the system has completely fulfilled expectations and contributed to a sustained increase in the quality of the rolling process."
reports Yves Unnützer, Online Measuring Systems Engineer at thyssenkrupp Rasselstein.
What makes the joint project, which has been in live operation since the end of last year, so special is the combination of two inspection technologies in just one system.
The advantages of this fusion of two inherently different technologies are obvious:
- The system’s 3D channel reliably detects serious defects such as shells, holes and wrinkles that can lead to broken strip or roll damage in the downstream process.
- The automatic depth measurement of the defects allows them to be clearly recognised and evaluated and thus reliably distinguished from harmless phenomena (e.g. soiling).
- In addition, the integrated 2D channel detects surface defects without height information, such as residual scale.
The 3D height measurement is based on the laser triangulation method. A laser line is projected on to the material surface, which is reliably detected by a camera positioned at an angle. Each pixel position in the image recorded by the camera correlates with a calibrated height position – a measuring principle that IMS has been using successfully in various systems for more than 20 years. High-precision lasers developed and produced in-house by IMS make it possible to display the height profile determined in this application as a coherent, high-resolution image.
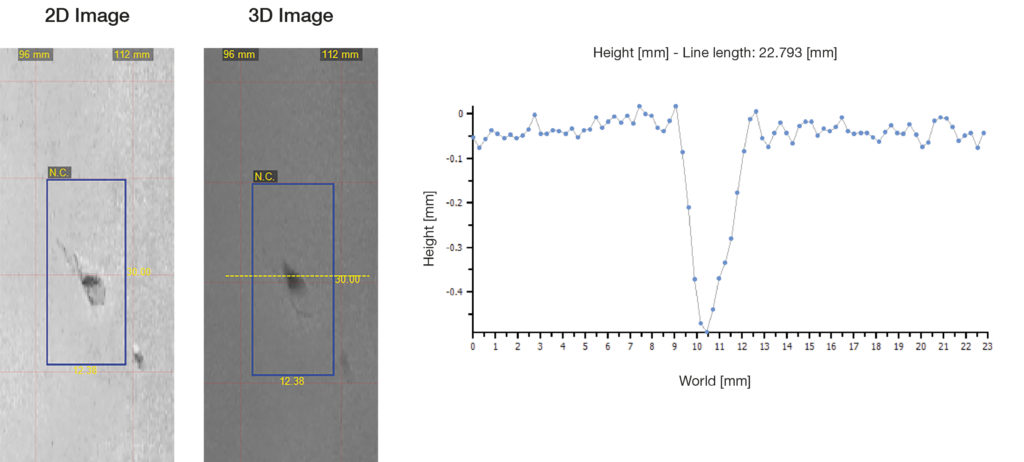