Customer Confirms Payback After Just 3 Years
Heiligenhaus, November 2024

- Exact determination of strip thickness profile as well as centreline thickness
- Based on the measurement results, the rolling mill can be controlled automatically and the production process optimised via a closed loop control
- Rolling mills produce cost-efficiently and according to the highest quality standards, delivering a flawless starting product to specification to the processing industry
Radiometric and optical measuring systems from IMS Messsysteme GmbH have been an integral part of the processes in steel rolling mills since the 1980s. Undergoing continuous development, each of these specific measuring systems contributes significantly to quality assurance in the manufacture of rolled products for the highest demands through 100% automated measurement, logging and documentation. Like the strip edge profile measuring system “Edge Drop”. Installed, for example, at the exit of a tandem mill, this system determines the exact strip edge thickness profile as well as the centreline thickness of the material.
It is a well-known problem: due to the rolling process, cold-rolled steel strip is thinner at the edges than in the centre. Customers, however, require a rolled end product with a thickness that lies within the tolerance range across the entire width of the strip.
For this reason, rolling mills produce with an excess width, whose size is based on empirical values. In this manufacturing method, the strip edges that fall short of the target thickness are trimmed off at the end of the production process in order to guarantee the required target thickness from edge to edge. From an economic point of view, however, this solution is anything but ideal, as it leads not only to increased material usage but also to a high level of waste, and thus to a cost-intensive material scrap rate and a poorer production result.
Deviations from the specified standard mean, therefore, in the worst case that the rolled end product is unusable for further processing as intended. In cold rolling mills, in particular, the risk of customer complaints is especially high if the profile thickness is out of the tolerance range. Only an end product with a uniform strip thickness that meets the specifications can guarantee its unrestricted suitability as a starting material for the processing industry. The IMS Edge Drop strip edge profile measuring system makes an economically compelling contribution to ensuring this
The most important parameter for the end product in cold rolling mills is the centre thickness of the strip. Classic 5-stand tandem mills therefore usually have a single-head centreline thickness measuring system before and after stand 1, as well as two redundant systems downstream of stand 5.
The Edge Drop strip thickness profile measuring system, by contrast, has three measuring heads. The middle measuring head, as in other thickness measuring systems, measures the strip centre thickness. What makes Edge Drop different, however, are the two outer measuring heads which can be moved independently of each other and fully automatically measure the respective strip edge thickness profile with high resolution.
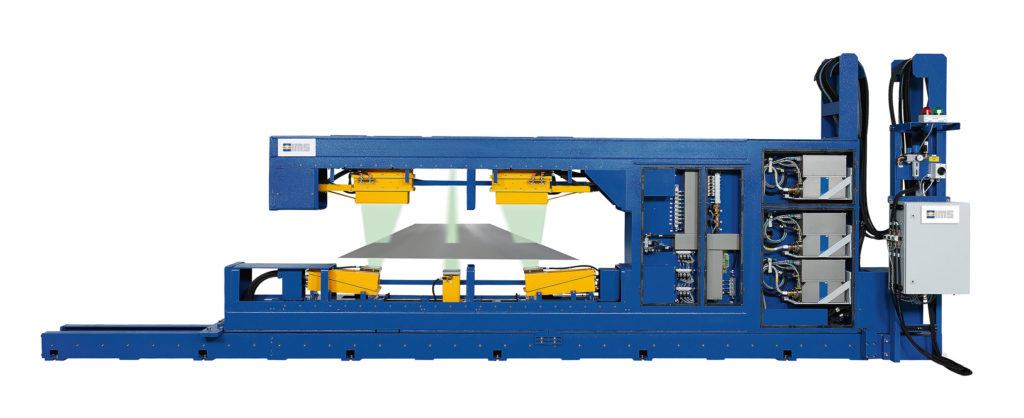
Just get
in touch.
You are interested in our Strip Edge Profile Measuring System (Edge Drop)?
Great! Let’s talk about.
Please do not hesitate to contact me if you require technical information or further explanations.
Sincerely,
Christian Knackstedt
Division Manager Sales & Marketing

Phone
As standard, the detector unit of the IMS Edge Drop installed in the middle measuring head comprises two or four detectors, while the two outer units have 15 or 22 detectors, although special solutions are also possible if required. Ionisation chambers are used as detectors. They convert the radiation that passes from the x-ray tubes through the material into electrical current. Using this residual radiation, or the current converted from it, the system determines the exact centre thickness and strip edge thickness profile.
The advantages of the IMS Edge Drop are therefore clear:
- The amount of trimmed material can be determined precisely from the measurement reports, which significantly reduces the scrap rate.
- At the same time, it is possible to control the rolling mill automatically with the help of the measurement results via a closed loop control, resulting in further optimisation of the production process.
Installed at the exit of the rolling mill, both the strip centre thickness and the strip edge thickness profile are thus determined with equal precision – and all this with just one Edge Drop strip edge profile measuring system.
Use of an Edge Drop strip edge profile measuring system is therefore a win-win solution for both the rolling mill and its end customers: the rolling mill produces cost-efficiently and in keeping with the highest quality standards, while the processing industry receives a flawless starting product that meets individual requirements.
Feedback from an Asian customer confirms the economic efficiency that use of an Edge Drop strip edge profile measuring system offers to rolling mills. In its tandem mill for silicon steels, the comparatively high initial costs of the IMS Edge Drop measuring system paid for themselves within just 3 years, solely due to the significant reduction in the scrap rate
However, the IMS Edge Drop measuring system is not only a benefit for steel rolling mills, but silicon rolling mills also profit decisively from its advantages. In this field in particular, highly exact thicknesses are crucial. In many of the end products produced there, several layers of the thinnest silicon steels are processed one on top of the other, such as in the manufacture of transformers. If the thicknesses of the individual layers are not connected homogeneously across the entire surface, the functionality of the end product may be impaired. The IMS Edge Drop determines and records the exact profile thickness even in these minimal thickness ranges, thus ensuring a high-quality and flawless product.
- Media
In our media area you will find supplementary image material of the
IMS Messsysteme GmbH for free use in the context of your public relations.
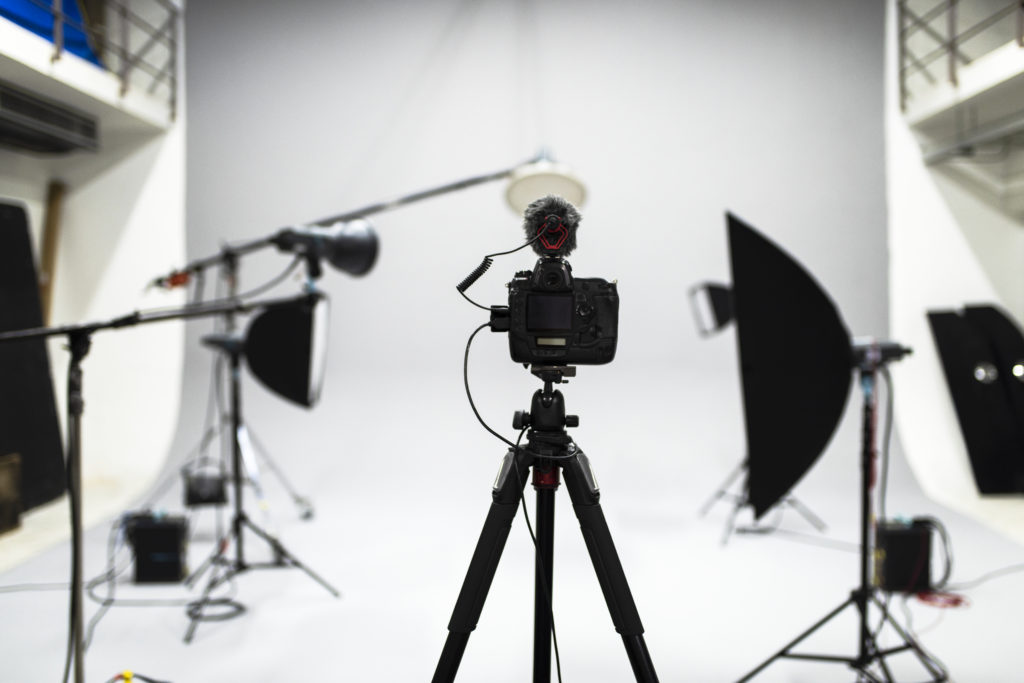
- Press Contact
Our responsible contact person for press & media will of course be happy to answer any questions you may have. We look forward to hearing from you!
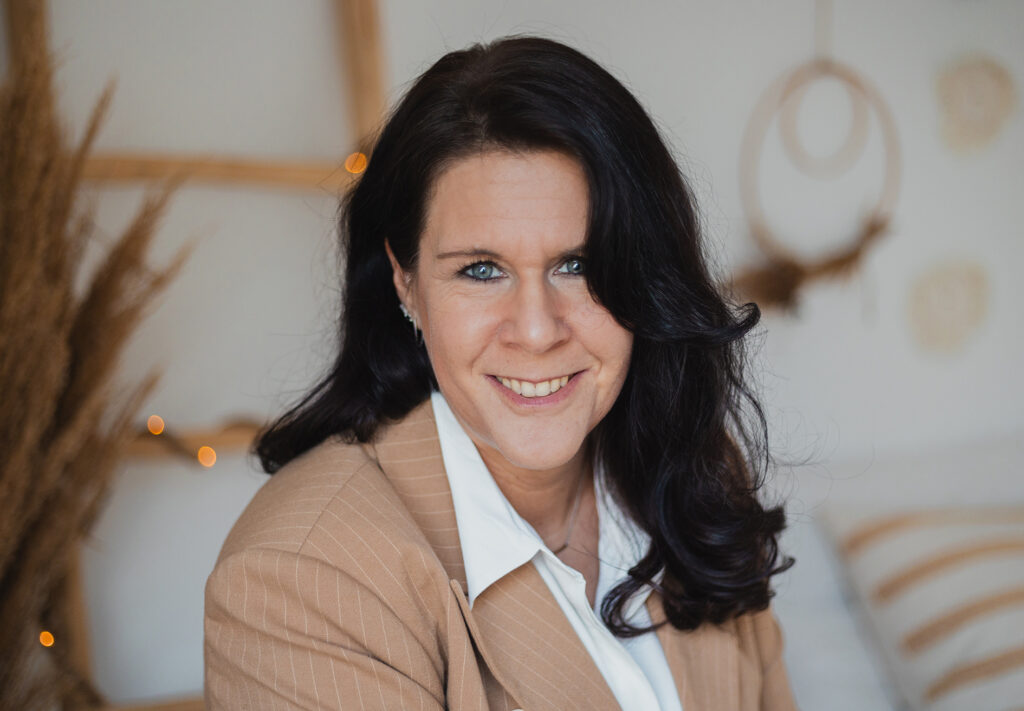
- sonja.koch@ims-gmbh.de
- +49 (0) 2056 / 975 - 228